
Delve into the fascinating realm of bronze, an enigmatic alloy that has captivated artisans and metalworkers for hundreds of years. Its attract lies in its distinctive sturdiness, malleability, and the fascinating hues it imparts, starting from gleaming gold to wealthy cocoa. Casting bronze, an historical artwork kind, empowers you to remodel molten metallic into beautiful sculptures, intricate jewellery, and enduring objects that transcend time. Embark on a journey of discovery as we unravel the secrets and techniques of bronze casting, empowering you to create fascinating artworks that may endure for generations to return. 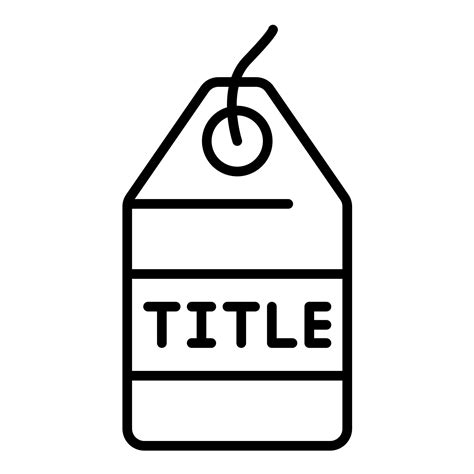
To embark on this enchanting journey, you’ll require a devoted workspace, important instruments, and an unwavering dedication to security. Your workspace ought to boast sufficient air flow, a sturdy workbench, and ample storage for supplies. Spend money on high-quality instruments corresponding to crucibles, tongs, and protecting gear to make sure a seamless and safe casting expertise. Prioritizing security is paramount; all the time put on acceptable protecting gear, together with gloves, security glasses, and a respirator, to safeguard your self from potential hazards. Together with your workspace meticulously ready and security measures in place, you at the moment are poised to unravel the secrets and techniques of bronze casting.
The essence of bronze casting lies within the harmonious fusion of copper and tin. By fastidiously manipulating the proportions of those metals, you may tailor the ensuing alloy to fit your particular inventive imaginative and prescient. Experiment with completely different ratios to attain a spectrum of hues, from the nice and cozy glow of gold to the deep patina of chocolate. The casting course of itself is a fragile dance of warmth and precision. Molten metallic, brimming with incandescent vitality, is poured into meticulously crafted molds, permitting it to solidify and tackle the intricate shapes you want. Via this transformative course of, you’ll witness the start of beautiful bronze sculptures, shimmering jewellery, and purposeful objects imbued with timeless magnificence and sturdiness.
The Metallurgy of Bronze
Supplies and Proportions
Bronze is an alloy primarily composed of copper and tin. The ratio of those metals determines the properties and purposes of the bronze. Conventional bronze is usually made with 88% copper and 12% tin, often called “88/12 bronze.” Bronze will also be alloyed with different metals, corresponding to aluminum, nickel, manganese, or silicon, to reinforce particular traits, corresponding to energy, corrosion resistance, or castability.
The invention of bronze marked a big development in human civilization, enabling the creation of instruments, weapons, and ornamental objects with superior energy and sturdiness in comparison with their stone and wooden predecessors. Bronze’s distinctive properties, together with its excessive energy, corrosion resistance, and ease of casting, have made it a significant materials in varied industries and purposes over the centuries.
Bronze is created via a course of referred to as smelting, which entails heating the copper and tin ores in a furnace to separate the metals from the impurities. The molten metals are then poured into molds to create desired shapes. The cooling and solidification course of leads to the formation of bronze, which may be additional labored and formed via casting, forging, or rolling methods.
The event and widespread use of bronze in the course of the Bronze Age ushered in a interval of technological developments and cultural transformations. It led to the emergence of specialised craftspeople and artisans, who performed an important position in shaping societies, selling commerce, and facilitating cultural exchanges.
Properties of Bronze
Bronze reveals a spread of properties that make it appropriate for varied purposes. It’s more durable and stronger than copper and has glorious put on resistance. Bronze can also be corrosion-resistant, making it superb for marine and outside use. Furthermore, it has good acoustic properties, making it appropriate for musical devices and bells.
Functions of Bronze
Bronze has been extensively utilized in quite a few purposes all through historical past. It was primarily employed for creating instruments, weapons, armor, and sculptures in historical occasions. In trendy occasions, bronze is broadly utilized in industrial equipment, architectural parts, marine fittings, musical devices, and inventive castings.
Property |
Worth |
Density |
8.96 g/cm³ |
Melting level |
933–1,083 °C (1,711–1,983 °F) |
Tensile energy |
300–700 MPa |
Hardness |
Brinell 120–250 |
Corrosion resistance |
Glorious |
Alloying Copper and Tin
To create bronze, copper and tin are mixed in a course of referred to as alloying. The proportions of every metallic within the alloy decide the precise properties of the ensuing bronze. Usually, bronze consists of roughly 88% copper and 12% tin, though variations in these percentages can produce completely different alloys with distinctive traits.
The method of alloying copper and tin entails heating the metals collectively till they soften and kind a homogeneous combination. This molten alloy is then poured right into a mould to create the specified form. Because the alloy cools, it solidifies and types bronze.
Refining the Alloy
As soon as the copper and tin have been alloyed, the ensuing combination might comprise impurities or undesirable parts. To take away these impurities, the alloy may be refined via a course of referred to as smelting. In smelting, the alloy is heated within the presence of a flux, which is a chemical substance that reacts with the impurities and causes them to separate from the alloy. The molten alloy is then poured off, abandoning the impurities within the slag.
The refining course of may be repeated a number of occasions to additional purify the alloy. The variety of occasions the alloy is refined will depend upon the specified degree of purity.
Casting Bronze Objects
Casting bronze objects is a fancy however rewarding course of. Step one is to create a mould of the article you wish to forged. This may be completed utilizing quite a lot of supplies, together with wax, rubber, or plaster.
As soon as the mould is made, it’s crammed with molten bronze. The bronze is then allowed to chill and solidify, and the mould is eliminated to disclose the completed object.
There are various completely different methods for casting bronze objects, however the most typical is the lost-wax methodology. On this methodology, a wax mannequin of the article is created after which coated with a layer of plaster. The plaster is then heated till the wax melts and flows out, leaving a hole mould. The mould is then crammed with molten bronze, and the bronze is allowed to chill and solidify. As soon as the bronze has cooled, the plaster mould is damaged away to disclose the completed object.
Misplaced-Wax Casting Course of
The lost-wax casting course of is a fancy one which requires an excessive amount of talent and expertise. The next are the steps concerned within the lost-wax casting course of:
- Create a wax mannequin: Step one is to create a wax mannequin of the article you wish to forged. This may be completed by carving the wax or by utilizing a mould.
- Create a mould: As soon as the wax mannequin is created, it’s coated with a layer of plaster. The plaster is then heated till the wax melts and flows out, leaving a hole mould.
- Fill the mould with molten bronze: The mould is then crammed with molten bronze, and the bronze is allowed to chill and solidify.
- Break free the plaster mould: As soon as the bronze has cooled, the plaster mould is damaged away to disclose the completed object.
The lost-wax casting course of is a flexible one which can be utilized to create all kinds of bronze objects. From small items of knickknack to giant sculptures, the lost-wax casting course of can be utilized to create lovely and distinctive artworks.
Misplaced-Wax Casting Strategies
Misplaced-wax casting, also referred to as funding casting, is an historical approach used to create bronze sculptures and different metallic objects. It entails making a wax mannequin of the specified object, which is then coated in a refractory materials to create a mould. The wax is then melted out, leaving a hole cavity that’s crammed with molten bronze.
The lost-wax casting course of usually entails the next steps:
1. Making a Wax Mannequin:
Step one is to create a wax mannequin of the specified object. This may be completed by carving the wax, utilizing a mould, or casting it from one other mannequin.
2. Constructing the Mould:
As soon as the wax mannequin is full, it’s coated in a refractory materials to create a mould. The mould is made from a cloth that may stand up to the warmth of the molten bronze, corresponding to plaster or ceramic.
3. Eradicating the Wax:
The wax is then melted out of the mould, leaving a hole cavity. This may be completed by heating the mould in a kiln or by utilizing a sizzling water tub.
4. Casting the Bronze:
As soon as the wax has been eliminated, the mould is crammed with molten bronze. The bronze is poured into the mould via a sprue, which is a small gap within the high of the mould. The bronze fills the cavity and solidifies, making a metallic duplicate of the wax mannequin.
Listed below are a few of the benefits of lost-wax casting:
Benefits |
Can produce extremely detailed and complex objects |
Can be utilized to forged objects of varied configurations and dimensions |
Is a comparatively exact casting approach |
Permits for a number of castings from a single mould |
The Artwork of Bronze Sculpture
Supplies for Bronze Sculpture
Bronze is an alloy of copper and tin, with different metals generally added to reinforce its properties and provides it a particular shade. The most typical sort of bronze used for sculpture is 85% copper and 5% tin, with the remaining 10% being a mixture of nickel, aluminum, manganese, or zinc.
Making a Bronze Sculpture
The method of making a bronze sculpture entails a number of steps, together with modeling, casting, and ending.
lost-wax casting
Misplaced-wax casting is a method of casting metallic sculptures utilizing a wax mannequin. The mannequin is comprised of wax after which coated with a mould. The mould is then heated till the wax melts and runs out, leaving a cavity within the mould that’s the identical form as the unique mannequin. Molten metallic is then poured into the cavity, and as soon as it cools and solidifies, the mould is damaged away, abandoning the metallic sculpture.
Trendy Strategies for Creating Bronze Sculpture
Along with conventional methods, there are a number of trendy methods that can be utilized to create bronze sculptures. These methods embrace sand casting, centrifugal casting, and electroforming.
Ending Bronze Sculpture
As soon as the bronze sculpture has been forged, it must be completed. The ending course of can contain sanding, sharpening, and patination. Sanding smooths the floor of the sculpture, whereas sharpening provides it a lustrous end. Patination is the method of making use of a chemical resolution to the sculpture to alter its shade.
There are various various kinds of patinas that may be utilized to bronze sculptures, and the kind of patina used will depend upon the specified impact. A number of the most typical forms of patinas embrace:
Patina |
Shade |
Pure |
Brownish-black |
Oxidized |
Deep black |
Inexperienced |
Greenish-blue |
Purple |
Reddish-brown |
Bleached |
Pale yellowish-white |
The Position of Bronze in Historical past
For hundreds of years, bronze performed a pivotal position in human historical past. Its distinctive properties made it an indispensable materials for civilizations across the globe, shaping technological developments and influencing cultural growth.
From Instruments to Weapons
Bronze’s distinctive energy and sturdiness made it an excellent materials for a variety of instruments and weapons. Bronze weapons, corresponding to swords, spears, and axes, gave armies a big benefit in fight. Bronze instruments, together with axes, hammers, and chisels, enabled civilizations to construct advanced constructions and develop refined crafts.
Bronze Age Civilizations
The event of bronze metallurgy marked the start of the Bronze Age in numerous areas of the world. These civilizations, such because the Babylonians, Egyptians, and Indus Valley civilization, skilled a interval of speedy technological and cultural development spurred by bronze’s availability.
Cultural Symbolism
Past its sensible purposes, bronze additionally held deep cultural significance. In lots of historical civilizations, bronze objects have been related to energy, wealth, and status. Bronze statues, collectible figurines, and jewellery have been usually used to depict gods, rulers, and different necessary figures.
Alloy Composition and Properties
Bronze is an alloy composed primarily of copper and tin. The ratio of copper to tin within the alloy determines its particular properties. Excessive-tin bronze is more durable and extra brittle, whereas low-tin bronze is softer and extra ductile.
Bronze Composition |
Properties |
Excessive-tin (15-20% tin) |
Onerous, brittle, appropriate for weapons |
Medium-tin (10-12% tin) |
Sturdy, sturdy, appropriate for instruments |
Low-tin (5-8% tin) |
Mushy, ductile, appropriate for castings |
Bronze as a Ornamental Materials
Bronze has been used for hundreds of years to create ornamental objects, from sculptures to furnishings. Its wealthy, heat shade and sturdiness make it an excellent materials for each indoor and outside use.
Bronze Sculptures
Bronze sculptures are a few of the most iconic and recognizable artworks on this planet. From the traditional Greek statue of Zeus to the fashionable works of Henry Moore, bronze sculptures have captured the creativeness of individuals for hundreds of years.
Bronze Furnishings
Bronze furnishings can also be extremely prized for its magnificence and sturdiness. Bronze tables, chairs, and different items of furnishings can add a contact of luxurious and magnificence to any room.
Bronze Mirrors
Bronze mirrors have been used for hundreds of years to mirror one’s picture. They’re usually adorned with intricate designs and may be present in quite a lot of sizes and styles.
Bronze Candlesticks
Bronze candlesticks are a gorgeous and purposeful method so as to add gentle to any room. They’re out there in quite a lot of types, from easy to ornate.
Bronze Vases
Bronze vases are a preferred selection for displaying flowers. They’re out there in quite a lot of sizes and styles, and may be present in each conventional and up to date designs.
Bronze Plaques
Bronze plaques are sometimes used to commemorate particular occasions or to honor people. They’re usually inscribed with textual content or pictures, and may be mounted on partitions or different surfaces.
| Bronze Plaques |
| ———– |
| Use | Commemorate particular occasions or honor people |
| Supplies | Bronze |
| Options | Usually inscribed with textual content or pictures |
| Mounting | Mounted on partitions or different surfaces |
Bronze in Structure and Engineering
Bronze is an alloy of copper and tin, and is understood for its energy and sturdiness. Bronze has been utilized in structure and engineering for hundreds of years, from the traditional Greeks to the current day.
Bronze in Historic Structure
Bronze was used for weapons, instruments, and armor within the historical world. It was additionally used to make statues, sculptures, and ornamental objects. A number of the most well-known historical bronze sculptures embrace the Statue of Zeus at Olympia and the Winged Victory of Samothrace.
Bronze in Trendy Structure
Bronze continues for use in trendy structure and engineering, however it’s now extra usually used for ornamental functions. Bronze can be utilized to make doorways, home windows, railings, and different architectural parts. It is usually used for sculptures and different artworks.
Engineering Functions of Bronze
Bronze can also be utilized in quite a lot of engineering purposes. It’s used to make electrical contacts, bearings, and different parts. Bronze can also be used within the automotive and shipbuilding industries.
Benefits of Bronze in Structure and Engineering
There are a number of benefits to utilizing bronze in structure and engineering:
- Power and sturdiness
- Resistance to corrosion
- Low upkeep
- Aesthetic enchantment
Disadvantages of Bronze in Structure and Engineering
There are additionally some disadvantages to utilizing bronze in structure and engineering:
- Excessive price
- Weight
- Will be troublesome to work with
Bronze Alloys
There are various completely different alloys of bronze, every with its personal distinctive properties. The most typical sort of bronze is copper-tin bronze, which accommodates between 88% and 92% copper and eight% to 12% tin.
Alloy |
Composition |
Makes use of |
Copper-tin bronze |
88-92% copper, 8-12% tin |
Basic goal bronze, used for castings, statues, and different purposes |
Copper-aluminum bronze |
80-90% copper, 10-20% aluminum |
Excessive energy and hardness, used for marine purposes, springs, and electrical contacts |
Copper-silicon bronze |
92-98% copper, 3-8% silicon |
Excessive energy and corrosion resistance, used for springs, electrical contacts, and chemical processing gear |
Trendy Functions of Bronze
Bronze is an alloy composed primarily of copper and tin. It has been used for hundreds of years in all kinds of purposes, each ornamental and purposeful. In recent times, bronze has seen a resurgence in reputation resulting from its distinctive properties. It’s sturdy, sturdy, and corrosion-resistant, and it has a gorgeous, heat shade that makes it superb to be used in each indoor and outside purposes.
Listed below are a few of the most typical trendy purposes of bronze:
Sculptures and artwork objects
Bronze is a well-liked selection for sculptures and artwork objects due to its energy, sturdiness, and talent to seize effective element. A number of the most well-known bronze sculptures on this planet embrace the Statue of Liberty, the Winged Victory of Samothrace, and the Discobolus.
Constructing supplies
Bronze is utilized in quite a lot of constructing supplies, together with roofing, siding, and window frames. It is usually utilized in inside design parts, corresponding to doorknobs, lighting fixtures, and furnishings.
Musical devices
Bronze is used within the manufacture of quite a lot of musical devices, together with cymbals, gongs, and trumpets. It is usually used within the strings of some guitars and violins.
Automotive elements
Bronze is utilized in quite a lot of automotive elements, together with bearings, bushings, and gears. It is usually utilized in brake pads and clutch plates.
Electrical parts
Bronze is utilized in quite a lot of electrical parts, together with connectors, switches, and contacts. It is usually used within the windings of electrical motors.
Jewellery
Bronze is utilized in quite a lot of jewellery, together with rings, bracelets, and necklaces. It is usually used within the manufacture of watches and different timepieces.
Medals and awards
Bronze is used within the manufacture of medals and awards, such because the Olympic medals and the Nobel Prize medals.
Different purposes
Bronze can also be utilized in quite a lot of different purposes, together with:
Bearing bronze is used for bearings and bushings, providing glorious put on resistance and conformability. Listed below are a few of the chemical composition particulars of bearing bronze:
Component |
Composition |
Copper |
75-95% |
Tin |
5-15% |
Nickel |
2-5% |
Lead |
0-5% |
Antimony |
0-1% |
Caring for and Preserving Bronze
Bronze is a sturdy, low-maintenance materials that may final for hundreds of years with correct care. Listed below are some suggestions for conserving your bronze gadgets wanting their greatest:
Cleansing Bronze
To take away filth and dirt, wipe down bronze objects with a comfortable, damp fabric. For extra cussed filth, use a gentle dish cleaning soap and water resolution. Rinse totally and dry with a clear fabric.
Sprucing Bronze
Over time, bronze can develop a patina, a pure protecting coating that may give it a novel character. In case you choose a brighter end, you may polish bronze with a comfortable fabric and a gentle metallic polish. Take a look at the polish on an not easily seen space first to make sure it doesn’t harm the bronze.
Defending Bronze from Put on and Tear
To stop scratches and dents, retailer bronze gadgets in a cool, dry place away from direct daylight. Keep away from utilizing harsh chemical compounds or abrasive cleaners on bronze.
Repairing Bronze
In case your bronze object turns into broken, it may be repaired by knowledgeable metalworker. Relying on the extent of the harm, the restore might contain welding, brazing, or casting.
Environmental Concerns
Bronze is a corrosion-resistant materials, however it will possibly nonetheless be affected by sure environmental elements. Keep away from exposing bronze to excessive ranges of moisture, salt, or air pollution.
Desk: Environmental Elements and Bronze Corrosion
Environmental Issue |
Impact on Bronze |
Moisture |
May cause pitting and corrosion |
Salt |
May cause accelerated corrosion |
Air pollution |
Can kind a boring patina that makes bronze seem tarnished |
Storage Concerns
To stop harm throughout storage, wrap bronze objects in acid-free tissue paper and retailer them in a cool, dry place. Keep away from utilizing plastic or rubber containers, as these can entice moisture and promote corrosion.
Show Concerns
When displaying bronze objects, select a location that is protected against direct daylight, warmth, and moisture. Use a comfortable fabric or dusting brush to take away mud and fingerprints repeatedly.
Common Upkeep
To keep up the great thing about your bronze objects, examine them repeatedly for indicators of damage or harm. Clear and polish them as wanted to forestall corrosion and protect their authentic look.
How To Create Bronze
Bronze is an alloy, which is a metallic made by combining two or extra completely different metals. Bronze is made by combining copper and tin. The proportions of copper and tin in bronze can fluctuate, however the most typical sort of bronze is 88% copper and 12% tin. Bronze is a powerful and sturdy metallic that has been used for hundreds of years to make quite a lot of objects, together with weapons, armor, and sculptures.
To create bronze, step one is to soften the copper. This may be completed in a furnace or a crucible. As soon as the copper is melted, the tin is added. The copper and tin are then stirred collectively till they’re fully blended. The molten bronze is then poured right into a mould. The mould is made from a cloth that won’t react with the bronze, corresponding to sand or plaster.
As soon as the bronze has cooled, it may be faraway from the mould. The bronze object can then be completed by sharpening, sanding, or hammering. Bronze is a flexible metallic that can be utilized to create all kinds of objects. It’s a sturdy and sturdy metallic that may final for hundreds of years.
Individuals Additionally Ask
What’s the distinction between bronze and brass?
Bronze is an alloy of copper and tin, whereas brass is an alloy of copper and zinc. Bronze is stronger and extra sturdy than brass, however brass is extra malleable and simpler to work with.
What are a few of the makes use of of bronze?
Bronze has been used for hundreds of years to make quite a lot of objects, together with weapons, armor, sculptures, and musical devices. Bronze can also be utilized in trendy purposes, corresponding to bearings, gears, and is derived.
How can I inform if an object is made from bronze?
Bronze is a reddish-brown metallic. It’s more durable than metal, however softer than iron. Bronze objects usually have a inexperienced patina, which is brought on by the oxidation of the copper within the bronze.